Plant Maintenance
We incorporate issues identified during routine maintenance and SDM (Shutdown Maintenance) into our designs, contributing to the optimization of maintenance and equipment.
After plant construction, during routine maintenance and SDM (Shutdown Maintenance), we address customer issues such as stable operation, energy-saving, rationalization, labor-saving, and external corrosion. These issues are tackled by design engineers (technicians) with extensive on-site experience and construction engineers (construction management technicians), thereby achieving problem resolution.
-
Our Company's Features
The distinctive aspect of our plant maintenance technology is the organization of a specialized design group within the maintenance department, focusing on maintenance, rationalization, energy-saving, and compliance projects for existing plants. We integrate customer feedback obtained from routine maintenance and SDM (Shutdown Maintenance), along with know-how in inspection and repair techniques, into our design philosophy. Viewing plant maintenance as a core business, we are actively expanding this area of our operations.
-
Routine Maintenance
In addition to promptly responding to issues that arise during equipment operation, we contribute to stable operation by providing suggestions for equipment improvement, coupled with emergency and permanent repairs.
-
Shutdown Maintenance
In SDM (Shutdown Maintenance), technicians well-versed in the maintenance techniques of a wide variety of equipment respond, suggesting safer and more efficient methods of maintenance. Furthermore, in equipment repairs, experienced construction managers and design engineers work together to accurately capture customer requirements and propose optimal repair methods.
Our Plant Maintenance Services (Examples)
- Ethylene Plant
- EO (Ethylene Oxide) & EG (Ethylene Glycol) Plant
- Various Polymer Plants
- Terephthalic Acid Plant
- Fine Chemical Plant
- Utility Equipment
- External Corrosion Inspection and Repair Work
- Tank Bottom Plate Replacement Work
- Rotary Dryer Inspection Work
- Equipment Diagnosis
For Customers Experiencing Difficulties with Maintenance and Equipment Diagnosis.
-
Stress Analysis
An example of stress analysis is interpreting the thermal stress on piping from thermography readings. From this temperature distribution, we predict the design fatigue life. In this case, when transporting powder from a hopper, the curved section of the elbow experiences localized high temperatures during operation, as shown in the figure below. The local thermal stress is calculated from the temperature distribution read from thermography, and the design fatigue life is estimated based on this.
-
Corrosion Under Insulation (CUI)
Corrosion under insulation (CUI) in the outer surface beneath insulation materials has become a significant problem in recent years, especially as a cause of accidents in aging petrochemical and chemical plants in Japan. Diagnosing CUI is challenging because the non-destructive testing techniques that can be applied vary depending on the condition of the target object, and it is said to be difficult with individual technologies alone. Our company is focusing on Acoustic Emission (AE), which is the elastic wave generated with the progression of defects, and we are working on CUI inspection. AE diagnostics can be measured while the plant is in operation and is applicable for CUI inspection under a wide range of conditions.
Corrosion Under Insulation (CUI) Inspection.
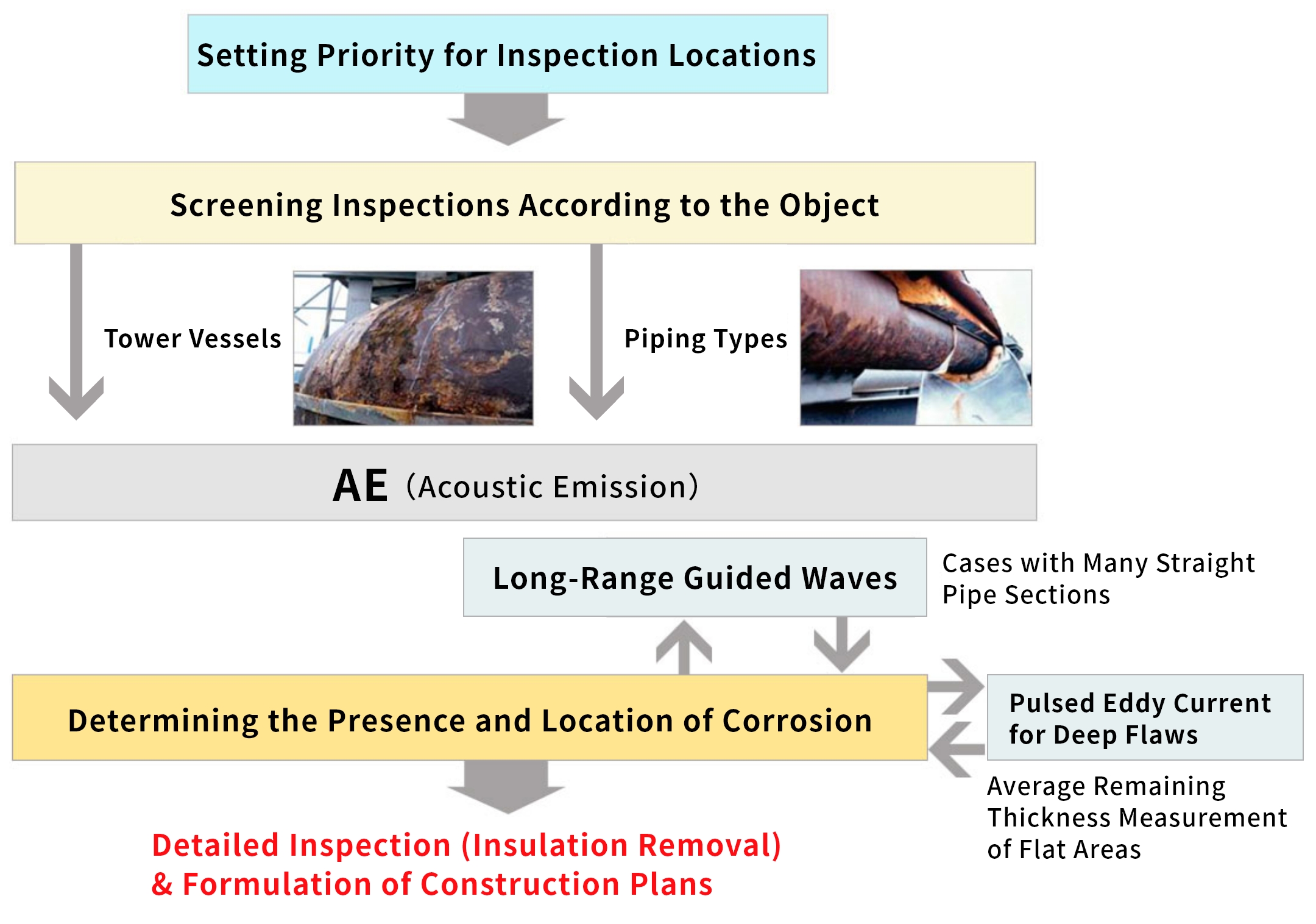